The CarbonFil Mars Rover – By Bart Gaczorek
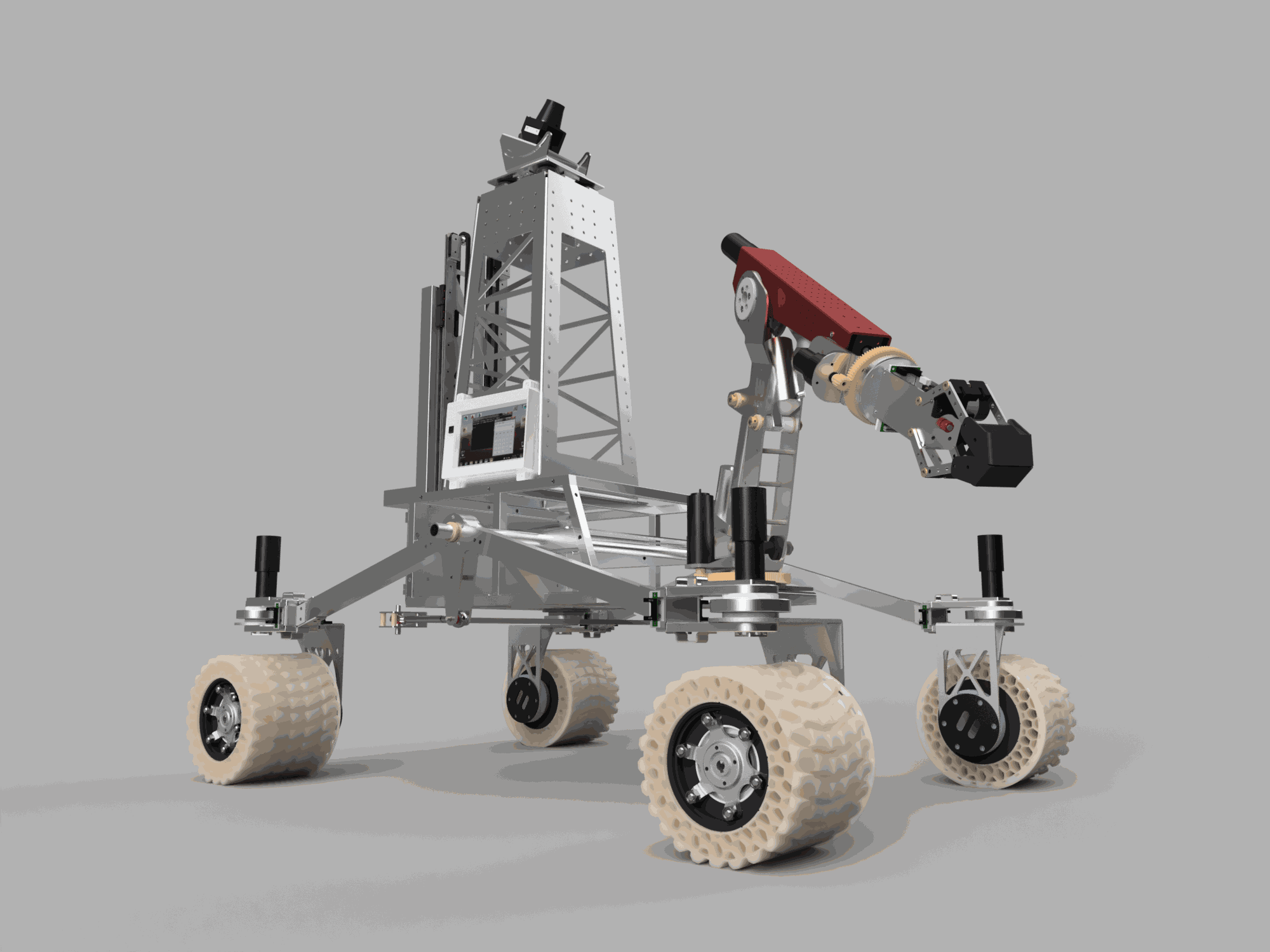
When I was asked by FormFutura about testing their CarbonFil composite filament at first I was quite in doubt. I was pretty sure I wouldn’t print another noone-really-neads-it thing like lo-poly Charmander or holder for GPS. I was aware of the unique engineering properties of the material and I really wanted to test it on real automotive application. I first contacted local Formula Student racing team but in a series of magical events I was surprisingly chatted up by AGH Space Systems student scientific club. After a brainstorm we decided to design and create innovative 3D printed propulsion system for their martian rover Kalman.
FormFutura provided all necessary filament for tests and final print of composite rims set. This summary covers work stretched over five months of tests, design changes, prototyping, 3D printing and assembling. All designs and prototype work on Kalman rover propulsion module was done by Andrzej Zakręcki (AGH Space Systems) and Bart Gaczorek (PLM Solutions).
Before I will start, I must say CarbonFil is the best adhering material I’ve ever used. Not only out of composite materials but of out all materials including modern and old-school PLA or TPU/TPE. It sticks incredibly well to warm Kapton tape covered with thin UHU stick glue layer, yet all the prints are super easy to remove from the build platform and to clean from minor support structures. I used large 10mm+ brim for all the prints and I’ve never experienced warping issues.
But on to the wheels… The aim of this project was to design and prototype stiff, durable and lightweight propulsion system for rover robot built by students. Common problem during last years competition was grip on diverse terrain. Stock RC car wheels used to completely loose traction on desert sand and slippery stones. Moreover, they are heavy and every single gram of space cargo costs a small fortune – lowering the weight means huge savings during real missions.
We decided to use the airless tire design derived from military applications and to place high-torque motor directly inside lightweight carbon rim.
Testing materials
We started out by testing on materials. The aim of the tests was to get structural buckling and static stress values and use them to enumerate Young’s module which is used to calculate part strength through Finite Element Method. I printed nearly 150 samples in two layer orientation and two infill densities (50% and 100%)that were born to die in tortures of squeezing, bending and stretching tests on top quality university metric equipment. Even though the test results values are lower than those by resin provider, they are still higher than we expected.
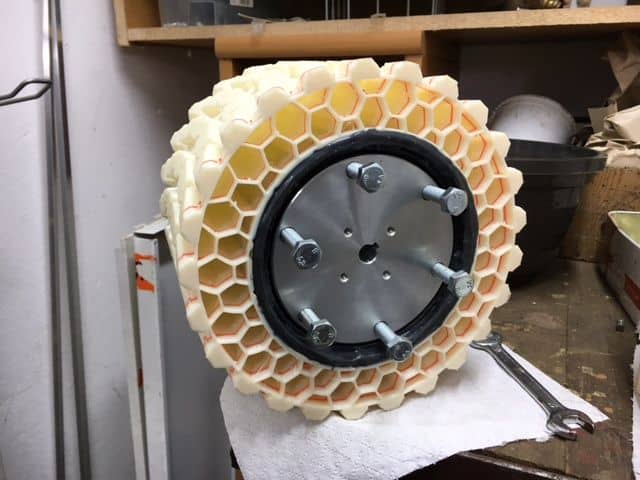
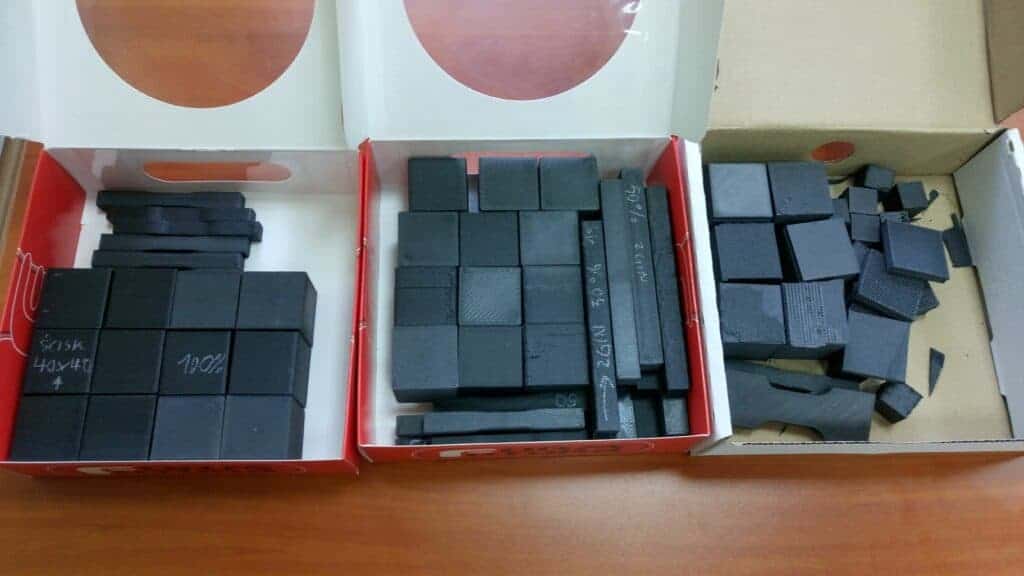
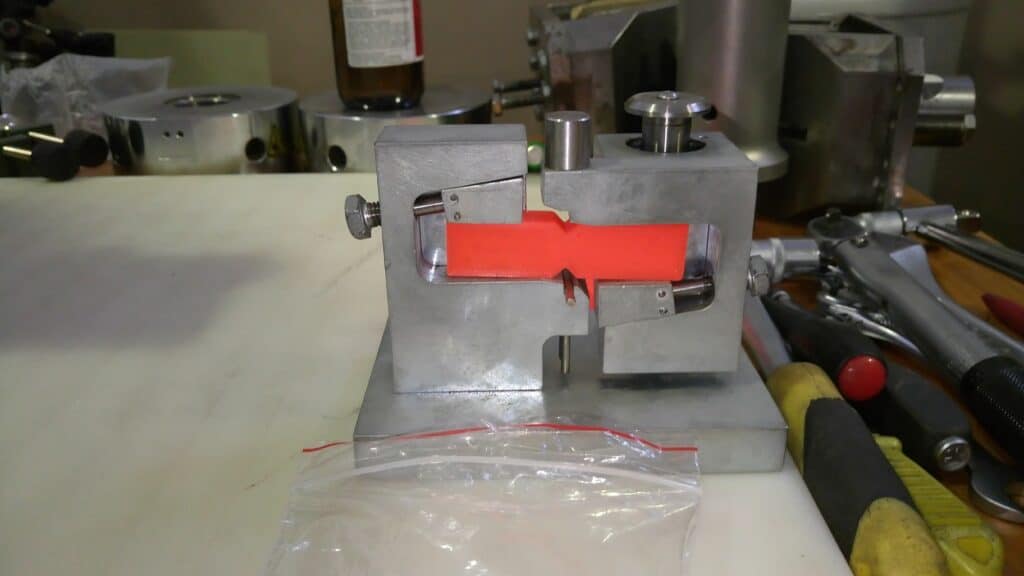
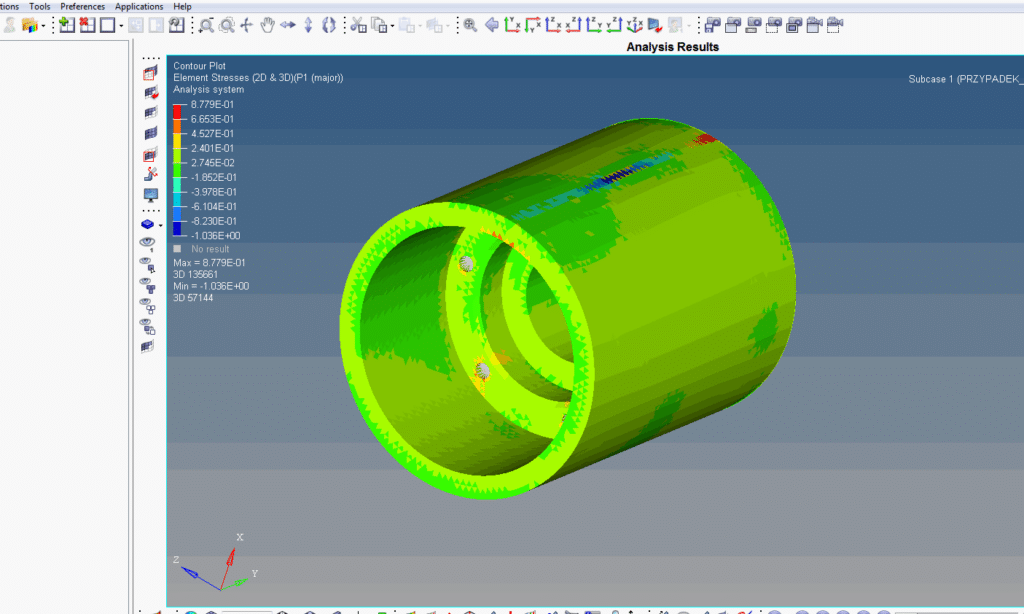
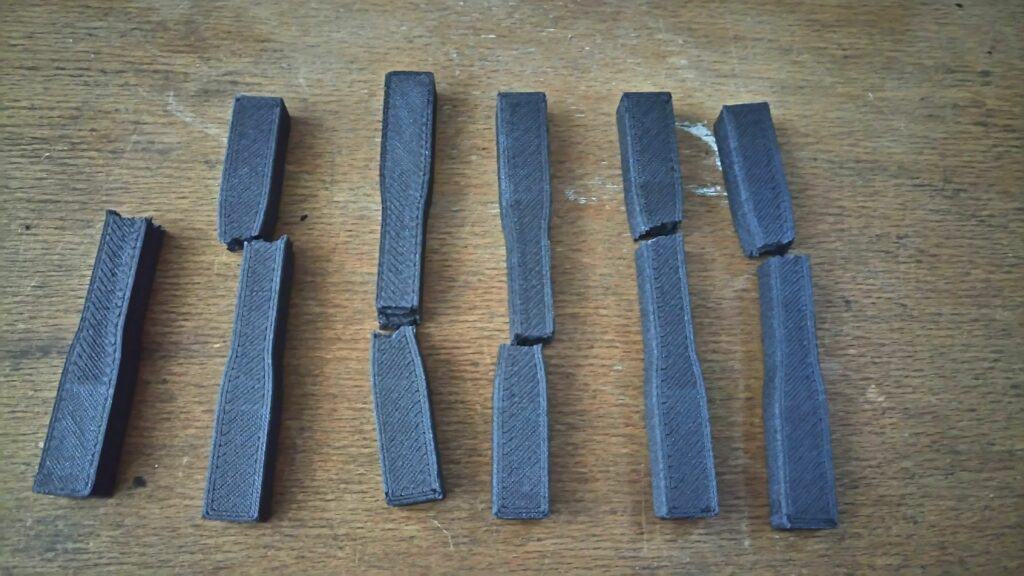
Full test summary will be available shortly.
I must confess I was considering carbon particles filled 3D printing filaments as a hype and I expected gain rather in stiffness than in strength. I was wrong but again reality occurs far more complicated.
We did some tests against plain HDglass and those were the most interesting. CarbonFil was lighter in every case, which is obvious. It was also stiffer and stronger on bending and stretching but surprisingly weaker on squeezing! So watch out for your layer orientation because its more important than ever! It is indeed more prone to pressure than HDglass, what can be observed during cleaning and machining final part. However, following the design guidelines the outcome was extremely durable parts!
To accelerate design process and give us more freedom I created a parametric algorithm for tire infill. Which is displayed on the right. I used Rhinoceros 3D with Grasshopper plugin. The density and orientation of honeycomb as well as wall thickness can be modified by only few sliders. Thanks to it we could test elasticity of some different samples and choose the best one.
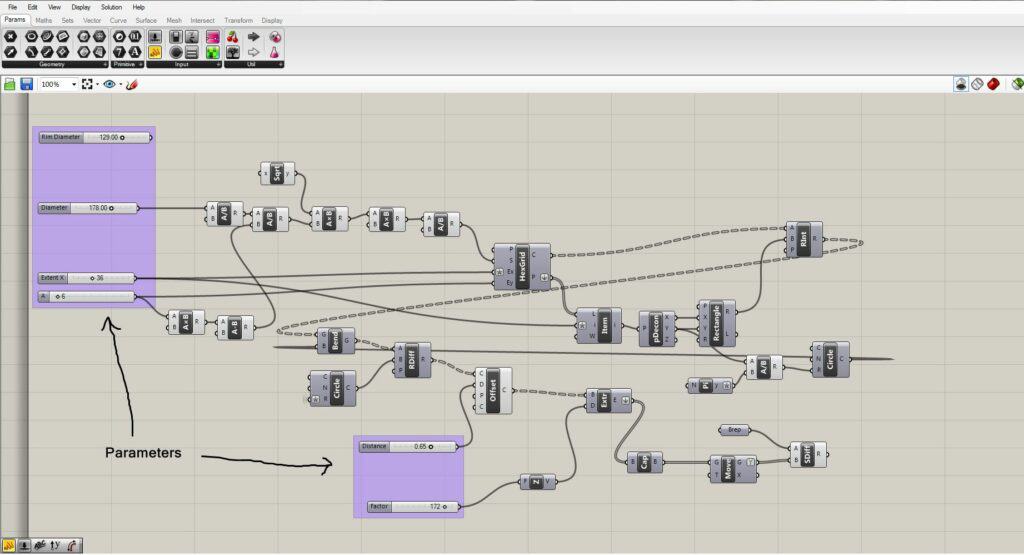
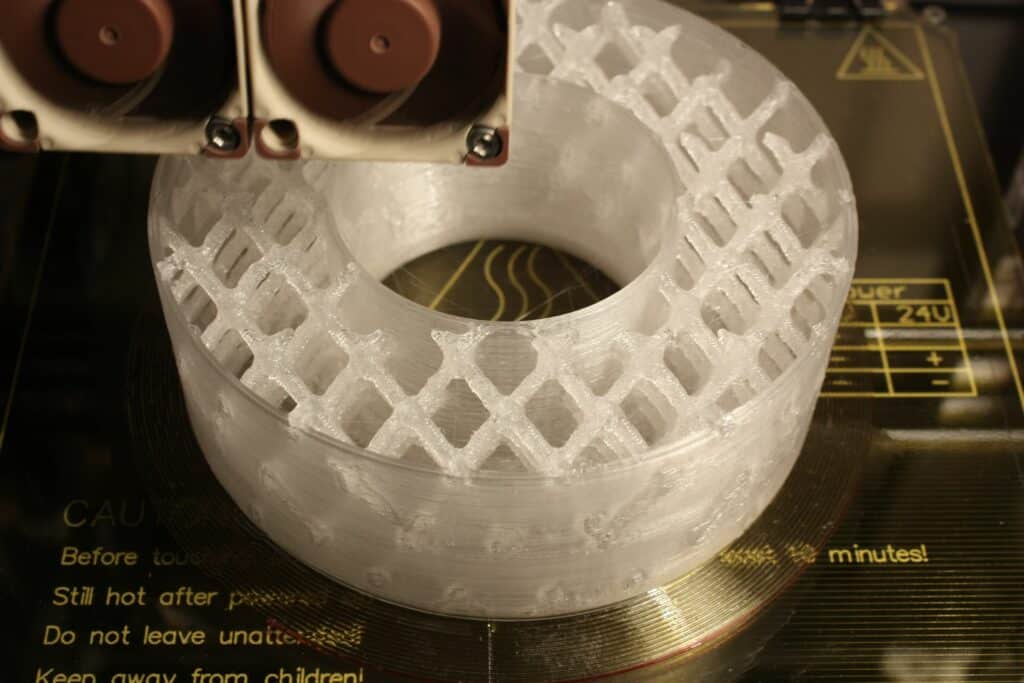
Rim structure during printing in HDglass for better visivility
For rim I choose lattice infill generated in Meshmixer. Weight and infill density is based on material tests results. I printed rim on 0.8mm hardened steel nozzle. Precision and retraction control were barely enough, but print time significantly decreased. CarbonFill tends to stick to nozzle and I had to pause print and manually remove “blackball” from time to time. This is the only noticed flaw of the material, otherwise prints rather easy.
The results were nice. The below table compares old and new wheel sets:
Old set | New set | |
Rim weight | 350 g | 300 g |
Motor weight | 1 800 g | 800 g |
Tire weight | 250 g | 700 g |
Total weight | 2 400 g | 1800 g |
Tire contact width | 90 mm | 150 mm |
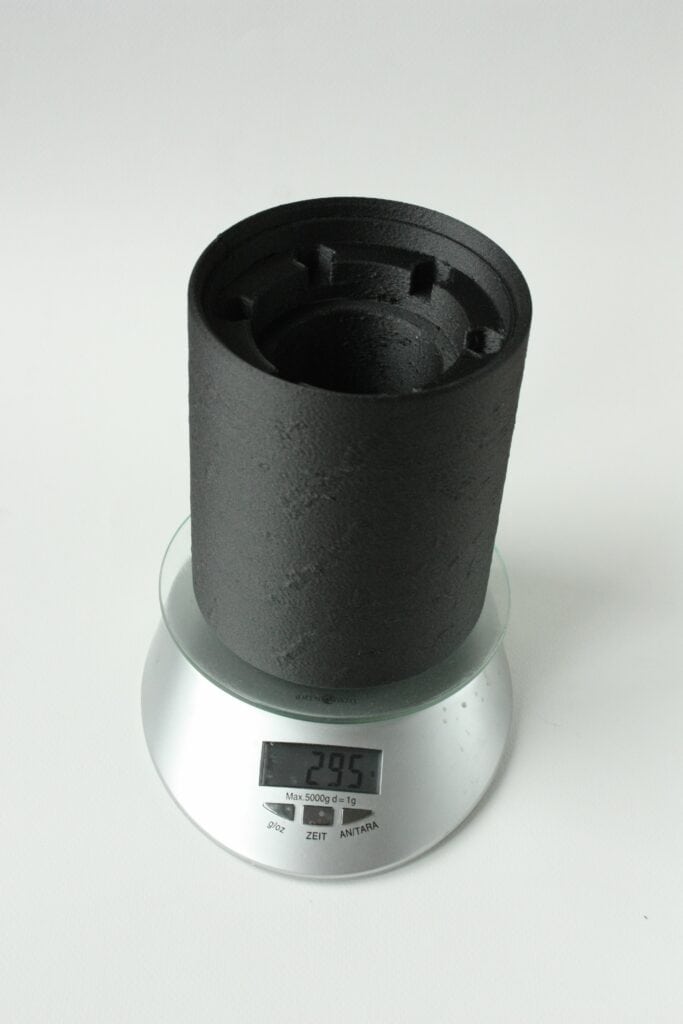
It looks as if we had paired new motor with old wheel we would have gained on weight the most. But we were not only looking for weight savings but also wheel grip and handling performance; we achieved both by widening the wheel and inserting the motor inside it. Better wheel design allows smaller motor to be used, so weight reduction comes directly from chosen materials and parts properties. In fact we would save nearly 2,8M $ on sending rover to the Moon*, not to mention Mars!
Working on this project has been a fantastic experience which proved that composite filaments are not just empty hype. Finally it was an opportunity to create something important, that can’t be created without help of 3D printing. This disruptive technology has changed the way we create things, now it slowly changes the way we design them. For sure 3D printing and generative design are one of the basic components of successful missions to Mars.
To sum up here are some quick impressions about CarbonFill:
- Very low shrinkage compared to Nylon based carbon filaments – surprisingly good adhesion to build platforms and even better removal.
- Retraction should be longer.
- It acts as if it swells – it’s visible that filament shrinks a few millimetres after nozzle – flowrate multiplier as low as 90-92%.
- It forms residuals on nozzle during print (very sticky). When especially large blob detaches on print it could cause print failure due to loosing steps or platform/nozzle shift.
*Estimation based on actual Astrobotic fares https://www.astrobotic.com/
About the authors:
Bartłomiej Gaczorek
Material tests and solid models by Andrzej Zakręcki
LinkedIn: