Hand in Hand NGO: Transforming Lives with 3D Printing
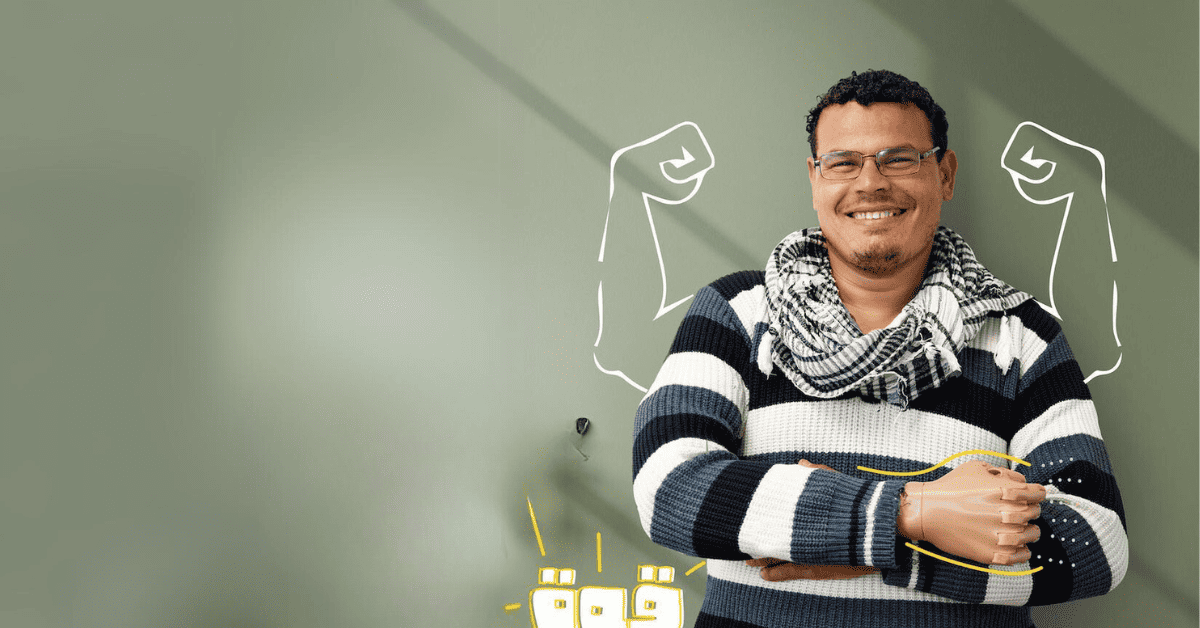
Hand-in-Hand NGO
In the realm of innovation, 3D printing stands as a beacon of endless possibilities! But there’s one story that goes beyond technology, one that resonates with compassion, empowerment, and a commitment to humanity. The tale of Hand-in-Hand, a non-profit organization based in Egypt, exemplifies how 3D printing isn’t just about cutting-edge manufacturing, but about transforming lives, dreams, and futures.
In this interview, we talked with Ayman from the Hand-in-Hand NGO. We talked about how they got started with 3D printing, why their work is so important, and how 3D printing is helping them change lives.
Below you can read and gain a better insight into the interview.
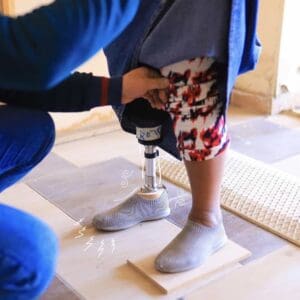
Please introduce yourself and tell us about your background and experience in the industry?
We are the Hand-in-Hand NGO. We’re a nonprofit organization based in Egypt. Egypt is a developing country with a high number of amputees. Due to the high cost of available prosthesis and the prevalence of low income and indigent communities in the country, many people are unable to afford a prosthetic device, which lowers their quality of life. Our aim is to enhance the lives of the Egyptian amputee population through providing them with 3D printed prosthetic devices for free.
Hand-in-Hand NGO was founded in September 2020. Our aim was to basically help and give back to the community. Our CEO Mohammed Hatab was diagnosed with cancer at the age of 9 years. During his treatment, he developed a sense of helping others, however due to his young age he was unable to pursue this until he graduated with a degree in Engineering. During his studies in the UK, he came across the process of manufacturing artificial limbs through his colleague studying Biomedical Engineering. This sparked his sense of aid once again, and consequently, he decided to integrate his field of study with Biomedical engineering to manufacture prosthetic devices in Egypt.
As such, he succeeded in developing upper and lower limb prosthesis using 3D printing technology and decided to donate these devices for free to people in need.
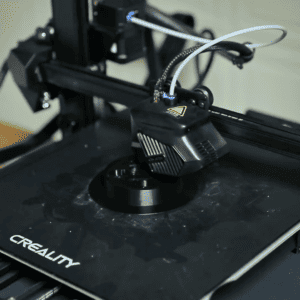
How did you become interested in 3D printing, and what led you to choose FormFutura’s products and services?
It was Mohammed, our CEO, who knew about FormFutura before, and then we got more acquainted with your 3D printing materials samples as we researched which material would be best to use. We were looking for a 3D printing filament that has durability and some flexibility. These are the main selling point, we need to have the amputees wear comfortable sockets. The idea came to use FormFutura’s PP or Polypropylene, and when we received the sample we decided to go ahead and send it to a lab in Belgium. This laboratory we work with is specialized to mimic the walking cycle of a human and tests between 5000 steps and 500,000 steps. The material and final print are very durable and there was no wear and tear, and it was actually very strong. We can provide you with that report.
That’s what we decided, that the FormFutura Centaur PP (Polypropylene) is a very good option. What also helped us make the decision to partner with FormFutura was that everyone was friendly and very willing to cooperate. So there’s cooperation, there’s vision and there’s the ability or willingness to help people, along with the high quality 3D printing materials.
How were prosthetics made before 3D printing?
It was a very tiring process, and very labor-intensive. The normal way prosthetics are made, is by making a cast. The person who will receive the prosthetic has to come in to make a model and they start. On average, the measurement would take 45 to 60 minutes. This is only if the person who takes the measurement to make the cast is working quickly. Then the casting takes place. The recipient is then covered with different kinds of materials. This process was a bit degrading, because they have to take off their clothes during the process.
We managed to do it in through 3D scanners and taking that measurement in 10 to 15 minutes without having them to just remove all their clothes. This process is actually much more customizable, time efficient, and it helps people in a more humane way.
A comfortable socket is one of the most important parts of the prosthetic itself. If the socket does not fit well, or if it’s uncomfortable, it is very hard to fix the problem. The amputee will either opt to not wearing the prosthetic, or he’ll just wear it and be very uncomfortable. For us that is that’s an emergency. It is comparable like if you bought a shoe that is too small and the fit does not match. It is then easy to get irritated.
As for the comfort of the material itself, prosthetics are usually made with higher end materials like carbon fiber, the problem is that these prosthetics are very expensive. That is why in Egypt most of the prosthetics use polyester, which is a very rigid material, unless you put some padding inside. Something that is, too rigid or too hard becomes uncomfortable quickly. Thanks to the Centaur PP that FormFutura is providing, the prosthetics have some flexibility, allowing the patient to be more comfortable.
What is the benefit of switching from manufacturing the traditional way to 3D printing?
There is a huge difference, but you have to look at it from different angles. Like we mentioned before, manufacturing the old way took a long time and was a bit degrading for the patient. It’s very labor-intensive and requires more than one person doing the work. Think of the many people doing the casting and the molds, and then finishing the socket. It can be done a lot quicker, but it costs a lot of money. With 3D printing, you can actually remove all these extra people. Two people who are designing these prosthetics, and taking these 3D scans. Using numerous 3D printers, we can actually do the work in 24 to 36 hours. So basically withing two days, you have gone all the way from a prototype to a fully finished product.
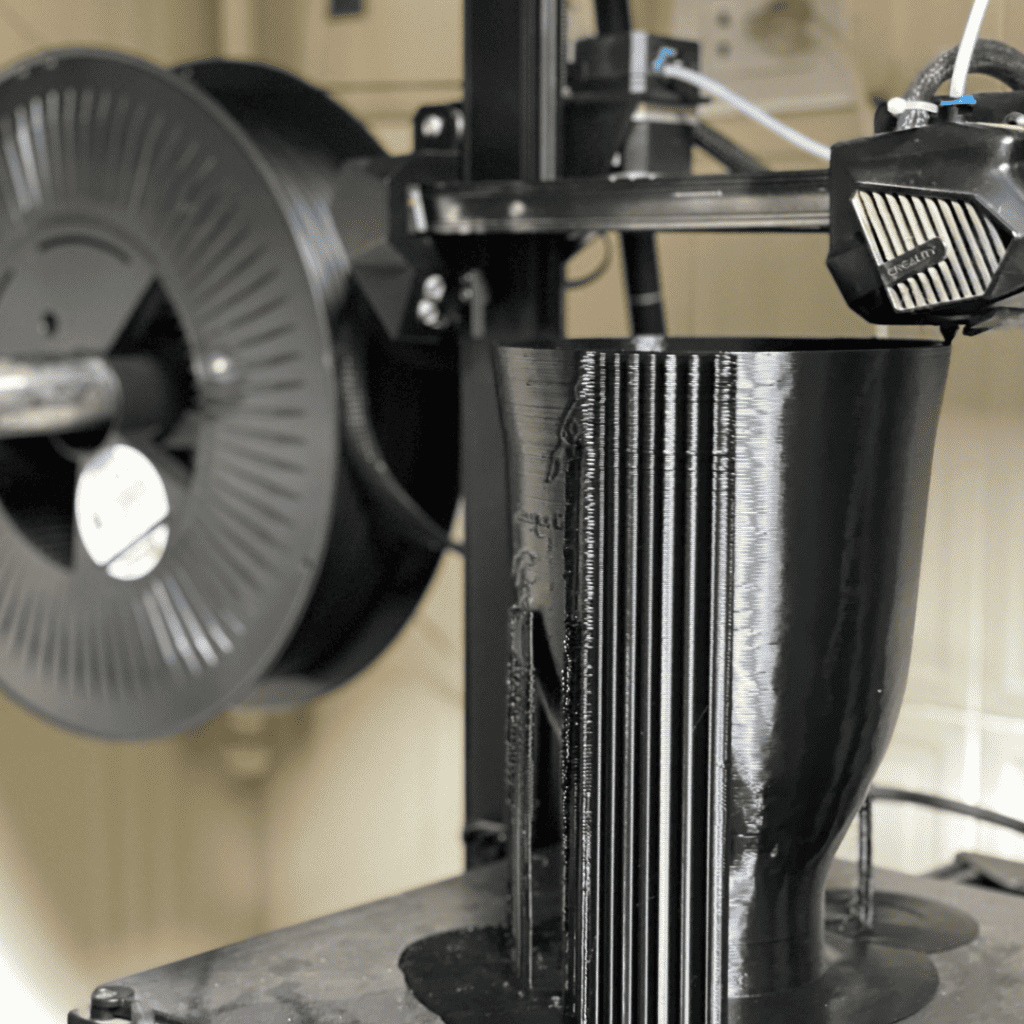
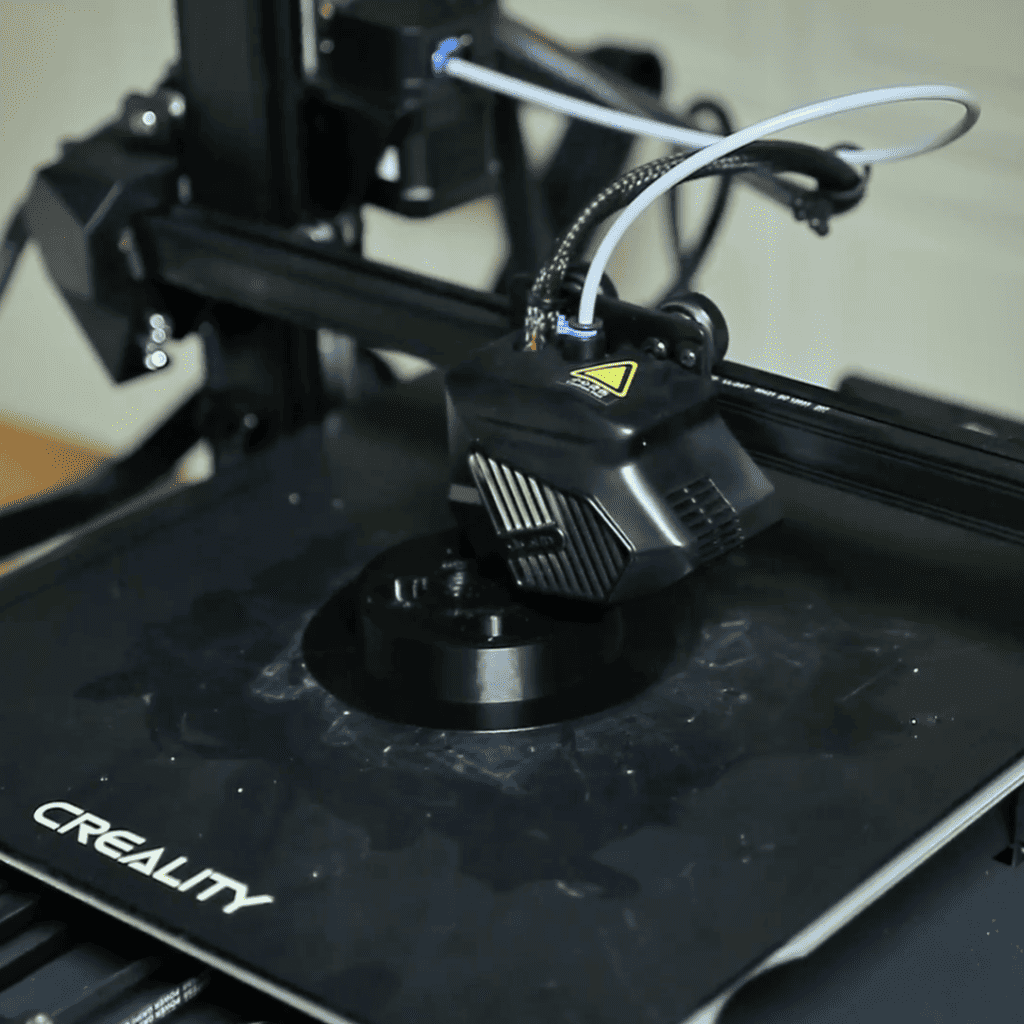
What types of prosthetics do you make?
We have three different types of products or devices. We have a full arm prosthetic, and then we have prosthetics for people with below wrist amputees, we have just the palms that functions similar to a hand. Currently, we are printing the trans radial part of the arm, this is the part of the arm below the elbow. Then there’s the final option for a below the knee device. All our prosthetics are 3D printed using Centaur PP, PLA and TPU.
What are the challenges you face during the 3D printing process, and how did you overcome these?
One of the challenges that we met in 3D printing was. When we started using the Centaur PP as it starts building, it would get unstuck from the bed. I think it is a common problem with 3D printing, and It caused a lot of problems and a lot of failed prints. That’s when we spoke to FormFutura, and you provided us with the PP glue sticks that you sell. When we started using that, it helped tremendously! It really helped us to finish and complete prosthetics. In the beginning, it was very frustrating. So that’s one big challenge that we managed to overcome.
What kind of unique advantages do you think 3D printing adds to your production course?
Firstly, it is much cheaper to work on a medium-sized scale, compared to large scale manufacturing. Large scale manufacturing is very hard when you have to produce customized parts in something like a factory. 3D printing, is much simpler than that. It all goes back to the G code. You can customize everything to every single patient on a broad scale.
So, in the past year and a half, almost two years, we have managed to help around 1400 to 1500 amputees. Another benefit of 3D printing is the weight of the prosthetics. It is always possible to change the infill, and you can do numerous things in layer height to actually make the device finished in a quicker way and be lighter.
Another factor for us is functionality. You can put 20 printers in one room, and that’s it. You have your own factory at home instead of wasting a lot of money and getting a huge space, or buying equipment.
What is the process patients go through to receive a Hand-in-Hand prosthetic?
We have a very straightforward process. We have different collaborations with NGOs, political parties and individuals as well, who provide us with the contact details of amputees. These patients then they get referred to our call center where they apply for a prosthetic through an intake interview. These intake interviews help us greatly to make sure that whoever comes through fits the requirement of the prosthetic that we provide. After the intake is approved, the patient is assigned a social caseworker. The social caseworker goes to their home, no matter where it is in Egypt. They check the living conditions and if this person meets the requirements to get a free prosthetic or if they are capable of paying a very small part as a donation.
If they get a preliminary approval, they get booked and get an appointment for an anatomical check assessment to make sure that the prosthetic would fit correctly. The next step is to take the measurements of the prosthetic. Part of what we provide is psychological help, we have a psychology team on board to make sure the patients are aware of the situation they are in, and what is about to happen. If the patient is then cleared to wear the prosthetic, we start manufacturing. In total, it takes us around a day or seven for that full cycle for people to come in at the psychologist, and taking measurement.
We try to deliver around 6 arm- and 28 leg prosthetics in one week, and we’re currently trying to expand the team. We’re trying to grow, so we can reach out, and help more people.
How important is it for these prosthetics to be available for free, and how do you manage to keep them affordable/free?
It is very important because when we started our research into the amount of amputees per local government, we found that there is an average amount of over 20,000 amputees per government. We also found out that there is a direct correlation between the social standard of living, the education and the number of amputees. That means that the better educated you are, the more you know about safety, and the more you take care of your health.
There are numerous things that help to prevent accidents. Unfortunately, as cruel as it sounds, poverty plays a huge role in these accidents. The people are put into situations that are unsafe and result in a high number of accidents. Awareness as well, the safety awareness is not being taught here. A lot of amputees come because of the gangrene from not taking care of their diabetes, for example.
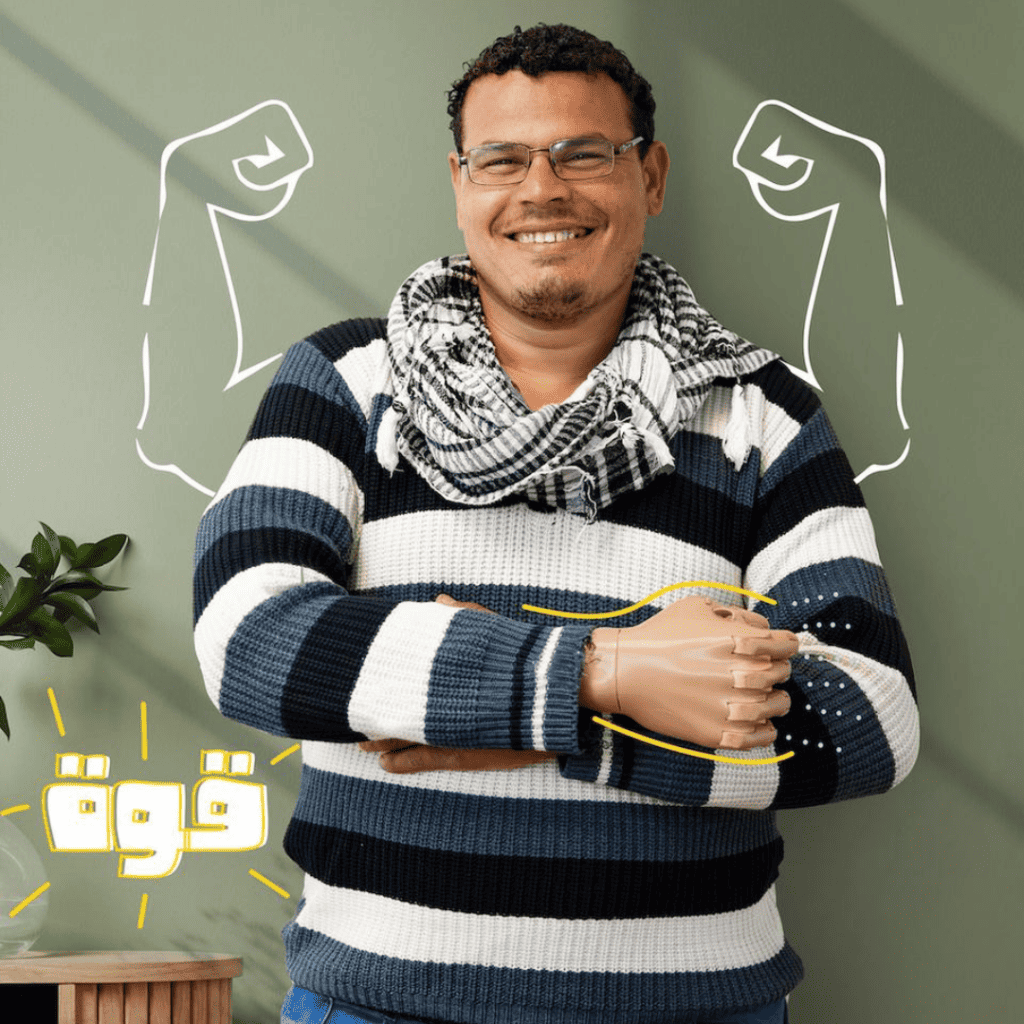
Currently, we’re just only able to help a very small fraction of the amputees. Our aim is to expand and to try to be located in every single government in Egypt and to be able to reach more people. Thanks to various collaborations, such as the one with FormFutura, we are able to run these operations. Our main source of income are donations, and we have a fundraising team that allows us to continue growing. They communicate with and convince different individuals, companies and different banks to support our cause.
Initially, the first two years, we were depending on individual funding and the board members of the Hand-in-Hand NGO. Then the people started to see that we were actually helping over 3000 amputees. They started seeing our presence on social media and more people started to watch our testimonial video’s. Later that year, people started to donate, and now we’re trying to be more self-sustainable through collaborations, donations, and fundraisers.
What are your plans for the future?
Our main goal currently is expansion. Not quickly, but swiftly. We want to make sure that everything is perfect. Recently we managed to perfect the lower limb, the upper limb and then when we’ve done that, we will start expanding to help more people in Egypt.
Our Long term vision is to expand globally. There are a lot of places in the world with wars and famine. We are sure that 3D printing is playing a big role in the future. You don’t have to even envision it. Everything is going to be 3D printed. Look at 3D printing. Three years ago, five years ago, six years ago, and look at it now, it’s rapidly evolving. It’s rapidly changing. It is being integrated in so many professions. It’s very easy, it’s very scalable, and it’s very cheap to just create samples instead of going to factories that that trade samples, it can be incorporated in numerous things.
How are people able to help the Hand-in-Hand NGO?
There’s the most basic way, which is donating. We have online links if people want to donate.
If donating is not an option, we appreciate the publicity people give us by sharing our website, social media posts etc. It is important that the people will get to know us, and that there is an NGO doing this type of work, trying to help people. That’s the vision our CEO has embedded in all the employees here. It doesn’t matter where they’re from, what they do, someone who’s here, you’re going to help them, and you’re going to make sure that they have a better life. Give them a chance to join back their communities.
If you are interested in helping the Hand-in-Hand NGO, please visit their website and make a donation!
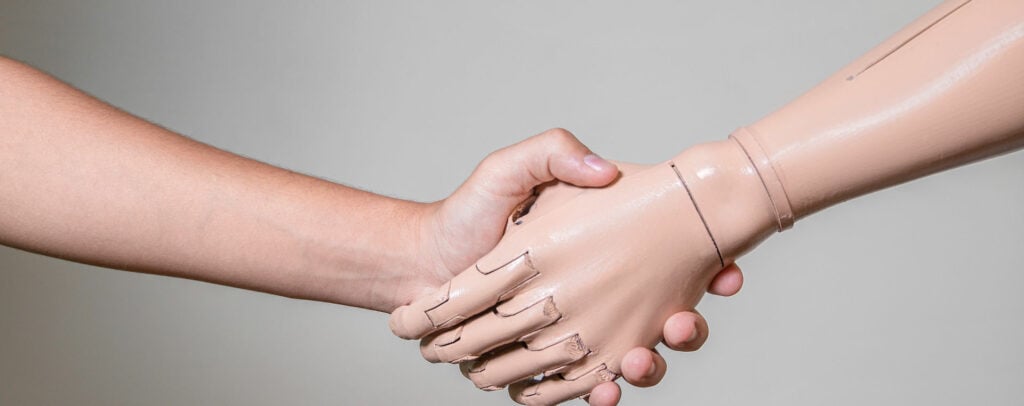
Contact
Contact Hand-in-Hand if you are in need of a free prosthetic device,
or if you want to donate to help us.
Adress: 43 Tanta Street, Agouza, Giza, Apt. 7, Third Floor
or
75 Abdel Moneim Riad Street – Agouza – Giza (Apartment No. 4 on the second floor – next to Faisal Islamic Bank)
Emai: info@handinhand-ngo.com
Web: www.handinhand-ngo.com