Achieve top performance with Speecos 3D printed handlebars
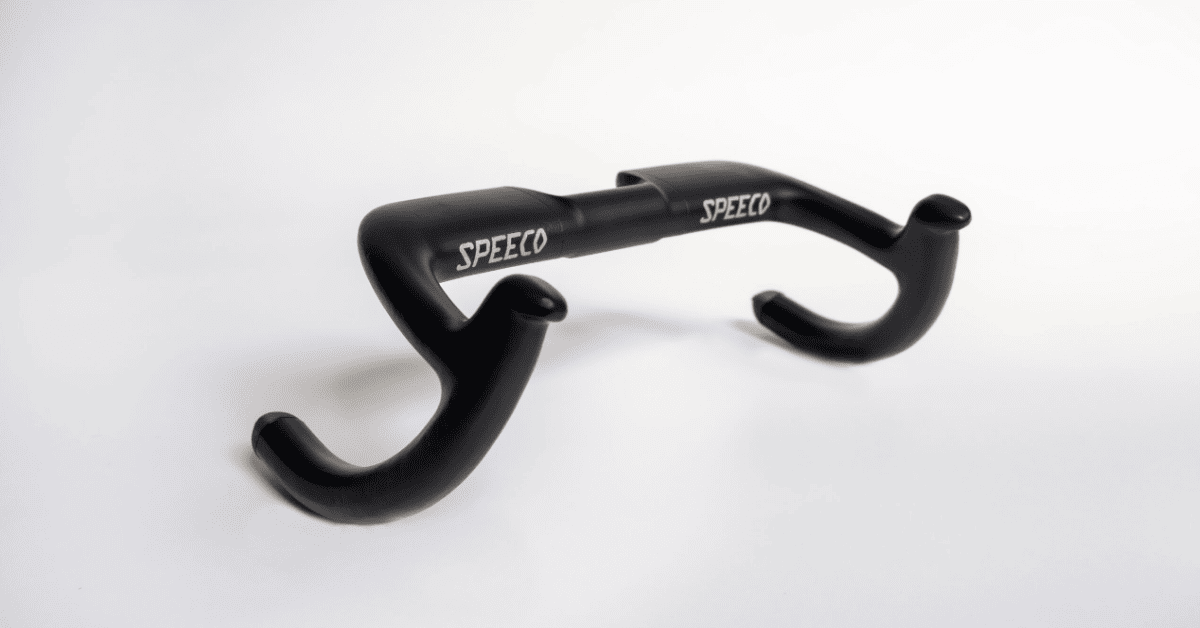
Estimated reading time: 7 minutes
The Pursuit of Excellence
Founded in 2022, Speeco is rapidly emerging as an industry-leading manufacturer of bespoke handlebars and aerobars. Cycling, being a sport shaped by countless factors, propels competitive cyclists to seek solutions that balance diverse considerations such as peak power versus endurance, rolling resistance versus grip, weight versus aerodynamics, and price versus performance.
Fuelled by a passion for racing, technology, and craftsmanship, Speeco continuously explore technological advancements and push the boundaries of conventional rules. Through intelligent processes and manufacturing methods, they aim to provide you with a fully customized product, regardless of your location. The team, led by founder Noah van Horen, alongside Product Designer Kai van den Brink and Product Engineer Job Visser, are committed to delivering nothing but the best.
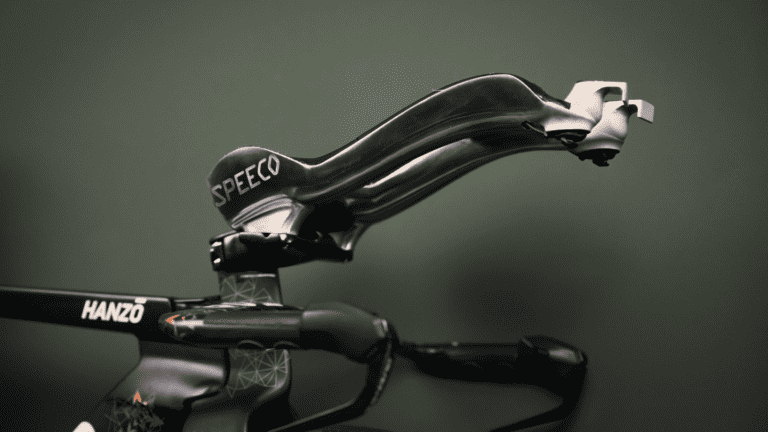
Meeting FormFutura
I got acquainted with FormFutura through Alex from St Joris cycles, as we often collaborate and soon will share a studio. He recommended talking to the folks at FormFutura. Since the summer of 2023, I've been utilizing your filaments for my printing projects.
The "AHA moment"
Competitors typically craft components manually, relying on provided dimensions to fabricate a pedal, for instance. This process often incurs high costs, and customers have no means of verifying if the fit is precise. The ease of verification comes with 3D printing a plastic model first. Production takes a day, and we ship it out. Customers can then proceed with installation and testing, providing them with a secure and informed feeling before committing to purchasing an actual part. 3D printing has become more affordable and accessible, allowing for quick iterations, design, and testing without lengthy waits.
Better performance with Speeco handlebars
A time trial bike differs significantly from a regular racing bike, especially in terms of geometry—angles and dimensions of the tubes. The most prominent disparity lies in the seat tube angle, which is more upright in a time trial bike compared to the more reclined position in a racing bike.
The essence of time trial biking lies in solo performance rather than group dynamics. Crucial to this is the rider's position on the bike, which directly influences air resistance, the most impactful force. To minimize this impact, riders maintain a certain position by leaning on the handlebars. However, supporting this position for a long time can be uncomfortable. Speeco, with its aerodynamic and comfortable design, allows cyclists to sustain this position for longer durations, enhancing overall performance.
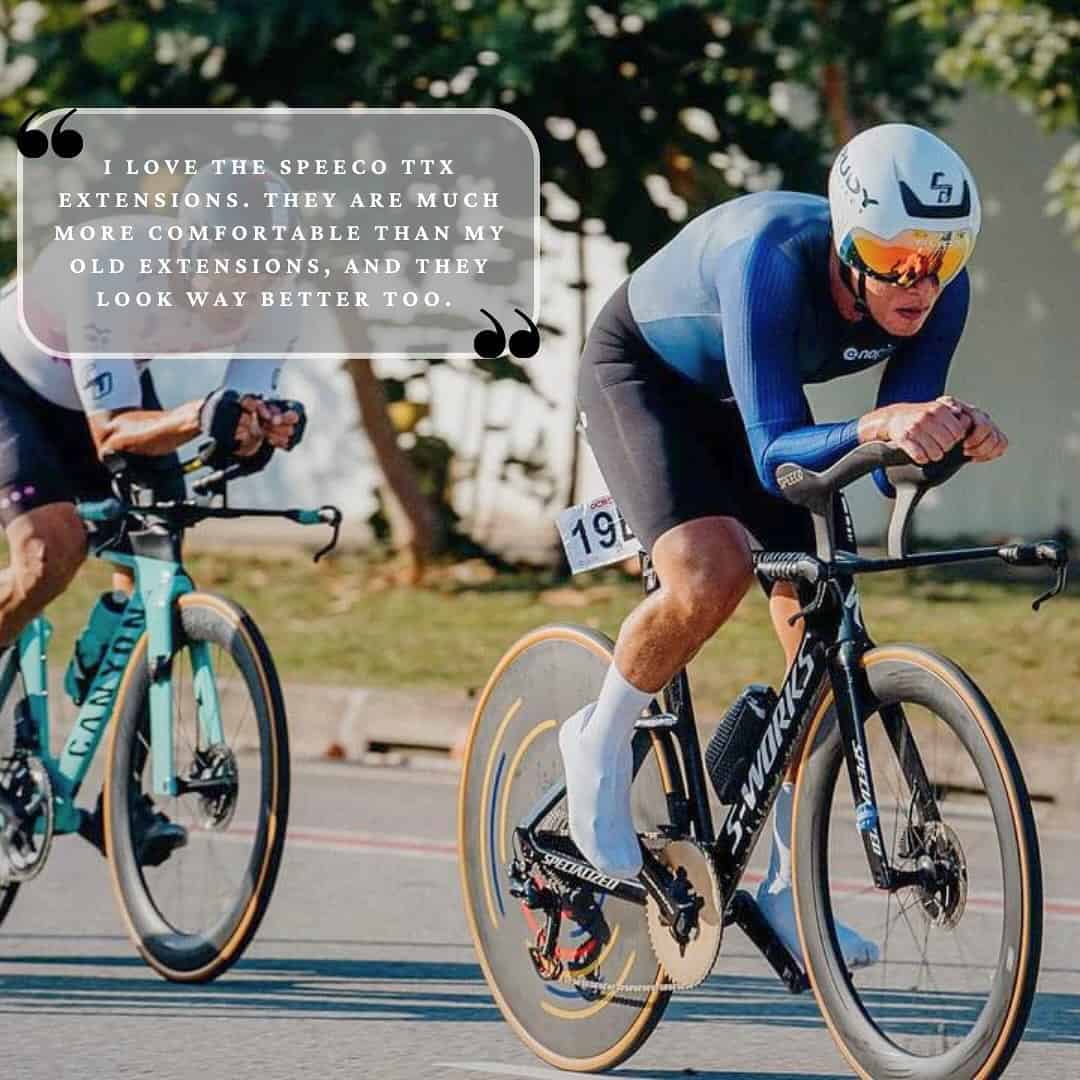
The Process, from prototype to final product
Primarily conducted online, we receive a measurement guide with 10 key points. These measurements are put into specialized software that generates a handlebar and optimal positions. The resulting model is then 3D printed using FormFutura's ReForm - rPET filament. While the measurement can be taken individually, it is recommended to involve a friend or a cycling physio specialist. We proceed to print the model, which is then shipped to the customer for testing. If the position is comfortable and fitting, the feedback is used to further refine the models. Upon final approval, the models are printed in aluminum, coated in various colors, and sent to the customer.
Picking the best material, rPET vs PLA
Given the bespoke nature of the models, they are designed for single-use. PLA was initially considered but proved too weak. The prototypes need to support the weight of a person without breaking. Additionally, cost-effectiveness is crucial in the prototyping phase, during which approximately ten kilograms of filament are used and discarded monthly. Discovering FormFutura's ReForm - rPET filament addressed both concerns by utilizing recycled materials and participating in a recycling project. All products sold in the Netherlands are returned, contributing to FormFutura's recycling program.
Comparing 3D printing with traditional production
The most significant advantage is the ability to work remotely. Previously, direct interaction with customers was necessary, but now, with 80 to 90 percent of our clients being international, they can provide dimensions from places like Singapore, and the models can be printed and shipped from the Netherlands. Self-producing prototypes is immensely beneficial as it allows us to control new options and features. Traditional methods involving aluminum molds and carbon fibers were expensive and lacked customizability. With 3D printing, we can have a prototype in hand within a day.
-
ReForm - rPET From € 8,26 Incl. VAT
Testing iterations for the perfect fit
For regular bespoke orders, we usually complete one model based on customer feedback. If significant changes are requested, a second prototype may be created. However, for entirely new products, iterations can extend to around 10, and for mass-produced versions in aluminum or plastic, potentially up to 100 iterations to fine-tune the design for serial production."
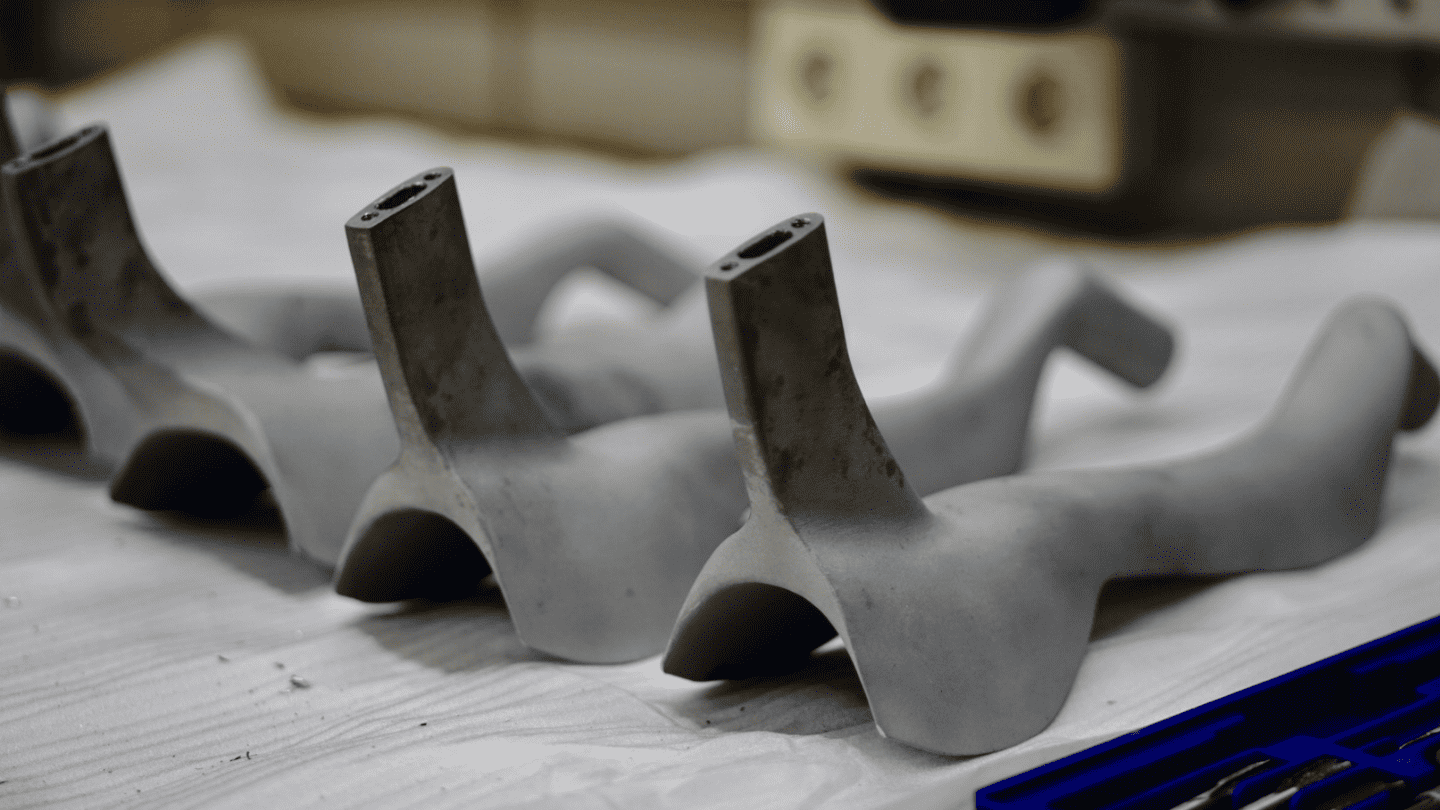
Challenges and Constraints
Entering a highly conservative market posed challenges, with the norm being to provide free materials before engaging in discussions. Offering plastic prototypes proved instrumental in swiftly convincing potential clients, easing entry, and reducing material and startup costs. This was especially impactful as we began Speeco as students, treating it as a hobby project. The affordability of 3D printing played a pivotal role.
FormFutura's contribution
Our collaboration with FormFutura, starting since the summer, has been crucial. Their recycled materials, combined with the recycling program, provided a sustainable solution, addressing the waste issue of discarding prototypes every month. The program significantly reduces our carbon footprint. Customization results in longer-lasting components, reducing waste. We plan to test various materials soon, including the new ReFill PETG.
-
ReFill PETG From € 14,04 Incl. VAT
Community, Collaborations and Partnerships
We work a lot with Alex of Sint Joris cycles, he is skilled in 3D CAD drawings. We played a vital role in advising and collaborating during the initial stages of 3D printing. We remain open to future collaborations, especially with partners who can supply us with high speed printers. Initially, I built the printers we use myself due to missing features, but the accessibility has improved, and spare parts are easier to obtain. Bambu Labs is an excellent option.
The Future of 3D Printing
Despite the advancements, I believe we haven't reached the pinnacle of 3D printing. A significant development would be a large-format Bambu Labs high-speed printer. In the cycling industry, 3D printing is increasingly utilized for end products, shifting from prototyping to producing complete printed bikes. While currently, this involves metals, the future might see fully printed bikes, possibly with materials like PEEK or other carbon-infused options. Improvements in layer adhesion, especially with materials like CarbonFil, present a significant opportunity.
-
CarbonFil From € 16,53 Incl. VAT
Speeco’s success story
We've had Olympic, world, European, and Dutch champions using our handlebars and seat posts. During the Tokyo Olympics two years ago, we produced all handlebars for the Norwegian team within eight weeks. I drove to Spain with a printer in the trunk, spending a week there. Three days were dedicated to training during the day, and in the evenings, I had prototypes ready for testing. Ultimately, Kristian Blumenfelt became an Olympic champion with Speeco, later achieving world champion status. The Dutch team has won titles in almost every discipline.
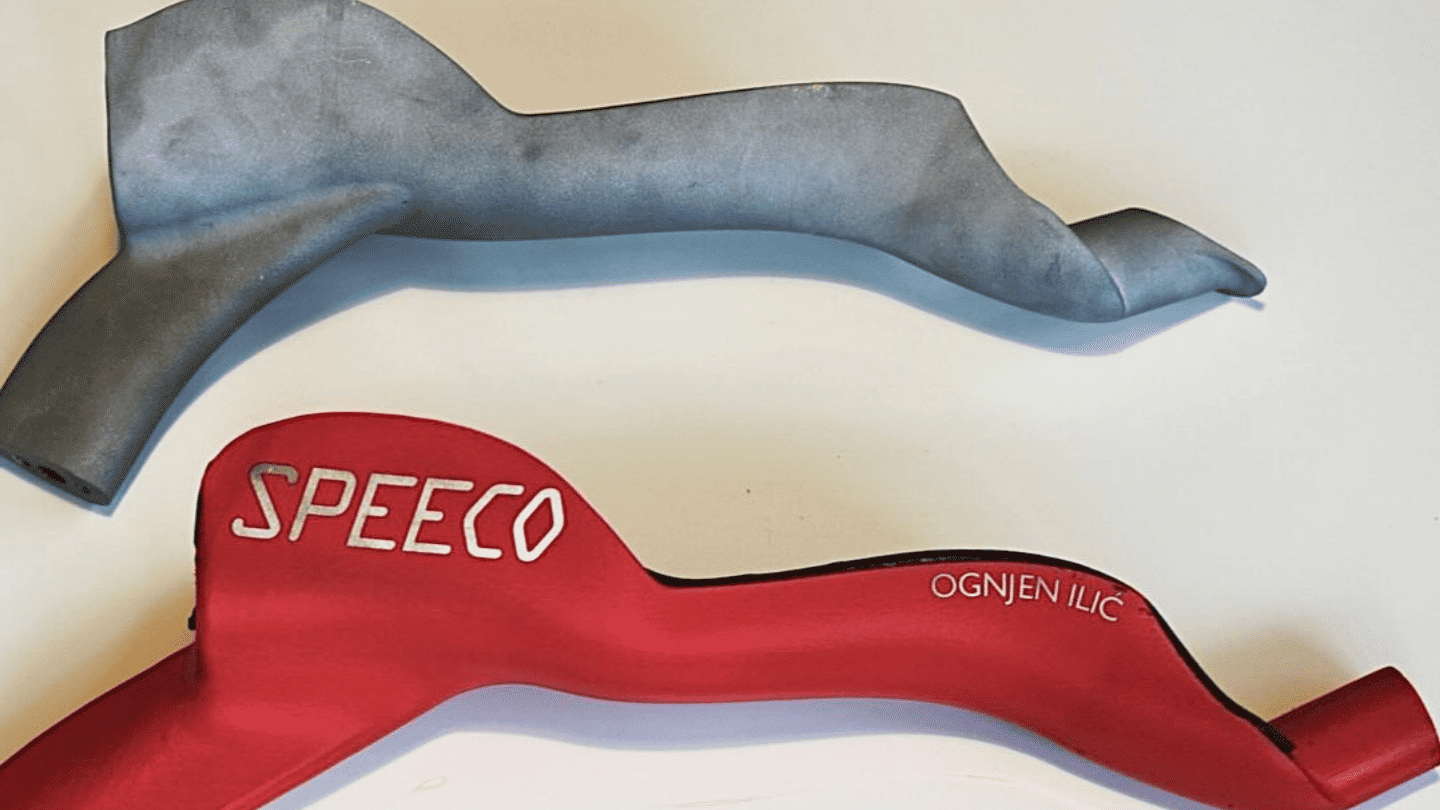
Market Insights
Currently, we are one of the four companies worldwide operating in this manner. The market is traditionally focused on carbon products, but for bespoke solutions, this isn't always the optimal choice. While two companies use carbon and one uses titanium, we specialize in aluminium, particularly emphasizing metal printing materials. The market perception often deems the winning material as the best ever, and anything else as subpar.
Preparations for the upcoming year are underway, with an increasing number of requests to test our products from individuals, teams, and national selections.
Incorporating 3D printing into your creative process
Start simple; don't make it overly complicated. Begin with the cheapest material available and experiment extensively before investing in pricier options. I learned this the hard way, purchasing an expensive printer with the idea that it would be foolproof, only to encounter issues. Understanding how a printer works and being able to maintain it yourself is crucial. Be prepared to see a mountain of plastic before achieving a satisfying final result.
Noah's Message
Look forward to spring when we kick off again. More information about Speeco can be found on our website or Instagram.